Geometric Dimensioning and Tolerancing (GD&T) is an internationally accepted language used to define and communicate engineering tolerances on parts and assemblies. It is used as an alternative to the traditional methods of manufacturing tolerances and dimensional control.
GD&T is an important part of a successful engineering career. It is used to ensure that the exact dimensions of an object are defined and communicated, and that these dimensions can be interpreted correctly. This ensures that the parts or assemblies created meet their intended function.
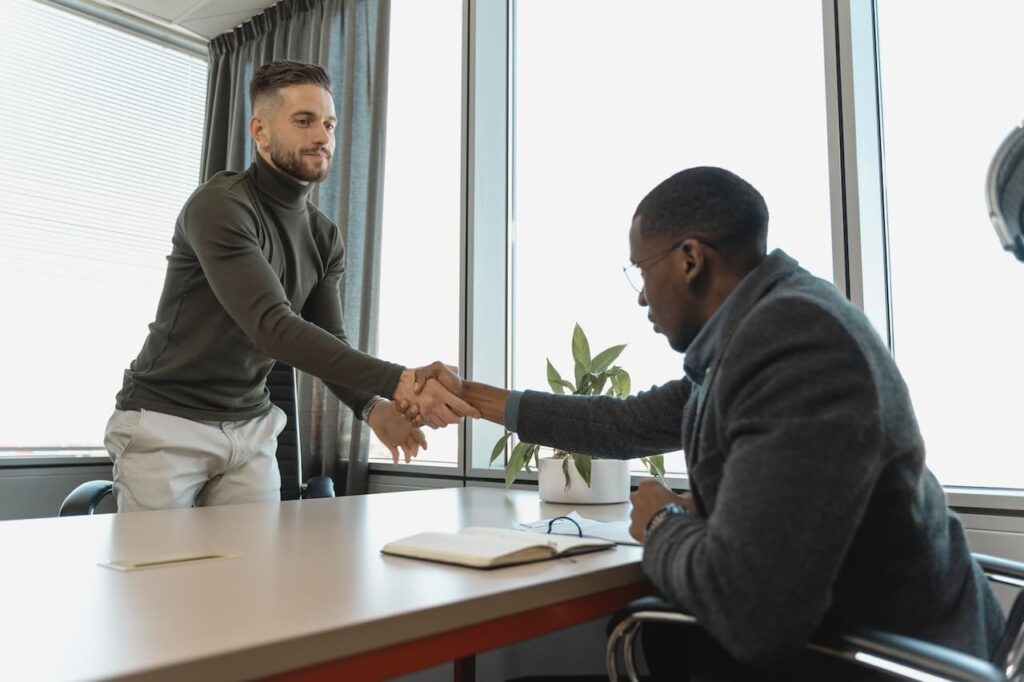
GD&T is a complex subject and prospective employers often use interviews to assess a candidate’s knowledge and understanding of it. It is essential that anyone looking to pursue a career in engineering should have a good grasp of the principles and applications of GD&T.
To help you prepare for a GD&T interview, we have developed this blog to provide an insight into the type of questions you may encounter. Our blog will also share in-depth answers to the questions, as well as some tips and advice to help you hone your interviewing skills.
By studying the questions and answers featured in this blog, you will be able to gain an understanding of the type of questions you may be asked, and how to answer them effectively. We hope that this blog will provide the knowledge and confidence you need to ace your GD&T interview and secure your dream job.
Overview of GD&T Interview Process
The GD&T (Geometric Dimensioning and Tolerancing) interview process is designed to determine the knowledge level of a candidate and to assess the candidate’s experience with GD&T. It is important to understand that GD&T is a specialized field and a candidate’s experience with GD&T is usually the most important factor in determining their success in the interview.
In most cases, the first step of the GD&T interview process is a phone screen. This phone screen involves a brief discussion between the candidate and the interviewer. During this call, the interviewer will ask the candidate questions about their experience with GD&T and their general understanding of the concepts. The interviewer may also ask the candidate to explain the basic principles of GD&T and the terminology associated with it.
After the phone screen, the candidate may be asked to take a GD&T exam. The exam is typically a written test that covers topics such as GD&T conventions, GD&T principles, GD&T symbols and GD&T calculations. The exam is designed to test the candidate’s knowledge of GD&T and to gauge their ability to apply what they have learned.
The final step of the GD&T interview process is the in- person interview. During the in- person interview, the interviewer will ask the candidate questions about their experience with GD&T and their understanding of the concepts. They will also ask the candidate to demonstrate their ability to interpret GD&T drawings, understand GD&T principles, and apply GD&T calculations. The interviewer may also ask the candidate to complete a GD&T task to demonstrate their proficiency in the area.
The GD&T interview process is designed to assess the candidate’s knowledge of GD&T and their ability to apply what they have learned. By understanding the process and preparing accordingly, a candidate can increase their chances of success in the interview.
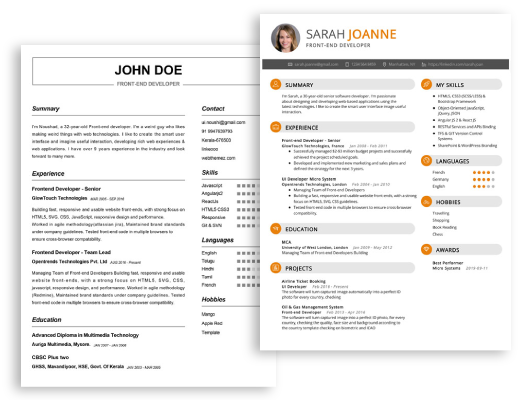
Start building your dream career today!
Create your professional resume in just 5 minutes with our easy-to-use resume builder!
Be sure to check out our resume examples, resume templates, resume formats, cover letter examples, job description, and career advice pages for more helpful tips and advice.
Top 25 GD&T Interview Questions and Answers
1. What is GD&T?
GD&T stands for Geometric Dimensioning and Tolerancing. It is a system used in engineering and manufacturing to precisely define the geometry of a product or part and the allowable variations in size and shape that can be manufactured and assembled. It is used to ensure that all parts are interchangeable and fit together properly, regardless of minor differences in size, shape, or orientation.
2. What is the purpose of GD&T?
The main purpose of GD&T is to ensure that parts fit together correctly and can be manufactured and assembled without difficulty. It also provides a common language for engineers, designers, and manufacturers to communicate their requirements. GD&T is used to ensure that parts can be produced to the required precision, without wasting materials or time.
3. What are some of the symbols used in GD&T?
Some of the symbols used in GD&T include the datum feature symbol, the tolerance symbol, the geometric characteristic symbol, the feature control frame, and the profile tolerance symbol. The datum feature symbol is used to identify a feature on the part that is used as the basis of the tolerances used in the design. The tolerance symbol is used to define the amount of variation that is allowed in a given dimension. The geometric characteristic symbol is used to identify a particular geometric feature of the part and any related tolerances. The feature control frame is used to define the exact tolerances that apply to a given feature. The profile tolerance symbol is used to define tolerances related to the profile of a part.
4. What is the difference between tolerance and GD&T?
Tolerances are used to define the acceptable range of variation for a given dimension or feature of a part. GD&T is a system used to define and communicate the exact tolerances that apply to various features of a part. GD&T is used to ensure that parts can be manufactured and assembled to the exact specifications required for the product. The use of GD&T helps to eliminate guesswork and misinterpretations in manufacturing and assembly.
5. What is a datum feature in GD&T?
A datum feature in GD&T is a feature on the part that is used as the basis of the tolerances used in the design. It is typically a flat surface, hole, or line that is used as a reference to ensure that other features of the part are located in the correct positions relative to the datum. The datum feature is usually the first feature referenced in the GD&T specification.
6. What is the difference between an orientation tolerance and a location tolerance?
An orientation tolerance is used to define the allowable variation in the angular position of a feature. It is used to ensure that the angular orientation of the feature is within a certain range. A location tolerance is used to define the allowable variation in the position of a feature. It is used to ensure that the feature is located within a certain range from the datum feature.
7. What is the difference between a primary and a secondary datum in GD&T?
A primary datum is the most important datum used to define the position of a feature. It is typically the first feature referenced in the GD&T specification. A secondary datum is used to provide additional positioning information for a feature. It is typically referenced after the primary datum.
8. What is the difference between a bonus tolerance and a non-bonus tolerance?
A bonus tolerance is an additional amount of tolerance that can be applied to the design of a part. It typically applies to features that are not critical to the function of the part. A non-bonus tolerance is a minimum amount of tolerance that must be applied to the design of a part. It typically applies to features that are critical to the function of the part.
9. What is the difference between a virtual condition and a true position?
A virtual condition is an imaginary reference line or point used to define the position of a feature. It is typically used in combination with other geometric tolerances to define a required position. A true position is the actual location of a feature relative to the datum feature. It is typically specified using the position tolerance symbol.
10. What is an axis in GD&T?
An axis in GD&T is an imaginary line used to define the orientation of a feature. It is typically defined using the orientation tolerance symbol. An axis can also be used to define the orientation of a surface.
11. How is GD&T used in manufacturing?
GD&T is used in manufacturing to ensure that parts can be produced and assembled to the required specifications. It is used to communicate the exact tolerances that must be applied to the design of a part. It helps to reduce waste and ensure that parts fit together correctly.
12. What are the benefits of using GD&T?
The main benefits of using GD&T include improved communication, reduced waste, fewer errors, and improved quality. The use of GD&T helps to ensure that parts can be produced and assembled to the exact specifications required for the product. It also helps to ensure that parts fit together correctly and that the proper processes and materials can be used in the manufacturing process.
13. What is the difference between a profile tolerance and a positional tolerance?
A profile tolerance is used to define the allowable variation in the profile of a part. It is typically specified using the profile tolerance symbol. A positional tolerance is used to define the allowable variation in the position of a feature relative to the datum feature. It is typically specified using the position tolerance symbol.
14. What is the maximum material condition and why is it important?
The maximum material condition (MMC) is the condition of a part in which all tolerances are at their maximum values. It is important because it defines the worst-case scenario in terms of the part’s dimensional accuracy. Knowing the MMC helps to ensure that parts can be produced and assembled to the exact specifications required for the product.
15. What is the difference between a perpendicularity tolerance and an angularity tolerance?
A perpendicularity tolerance is used to define the allowable variation in the perpendicularity of a surface or axis relative to a datum. It is typically specified using the orientation tolerance symbol. An angularity tolerance is used to define the allowable variation in the angle between two surfaces or axes. It is typically specified using the orientation tolerance symbol.
16. What is Geometric Dimensioning and Tolerancing (GD&T)?
Geometric Dimensioning and Tolerancing (GD&T) is a system of symbols used to define the desired size, shape, orientation, and location of a part relative to other features. It enables engineers to precisely specify the size, profile, orientation, and location of part features. GD&T is used to create part drawings that have more detail and contain more information than traditional drawings. GD&T provides a common language for understanding and communicating between engineers, designers, and machinists.
17. What is the difference between GD&T and regular dimensioning?
Unlike regular dimensioning, GD&T is a language used to describe how a part should be made, allowing for more tolerance and flexibility in design while still maintaining a certain degree of accuracy and precision. Regular dimensioning just gives exact size and shape measurements, while GD&T can give specific tolerances and orientations. GD&T allows designers to control the variability of a design within certain limits and to describe how two parts are related to each other.
18. What are the benefits of using GD&T?
GD&T is a powerful tool that enables engineers to accurately define the size, shape, orientation, and location of a part relative to other features. It eliminates ambiguity and ensures that the design is interpreted correctly, resulting in fewer design revisions. It also reduces manufacturing costs by allowing for tighter tolerance and less waste. Finally, it allows for improved communication between engineers, designers, and machinists by providing a common language for understanding and conveying design intent.
19. What is an datum plane?
A datum plane is a reference plane or surface used as a reference point for measurements. It is the standard from which other measurements are taken. Datum planes are used to orient the other features of a part relative to each other and to make sure that the parts fit together as intended.
20. What is a tolerance zone?
A tolerance zone is an area or region in which a part or feature must fall within certain parameters. It is defined by maximum and minimum limits that are determined by the designer. It is used to specify the allowable amount of variation of a part or feature.
21. What is a positional tolerance?
A positional tolerance is a GD&T symbol that specifies the allowable variation of a feature from its theoretical perfect position. It is used to describe the allowable deviation of a feature from its precise, nominal or true position.
22. What is the difference between a datum and a datum reference frame?
A datum is a reference plane or surface used as a reference point for measurements, while a datum reference frame (DRF) is a set of three mutually perpendicular datums used to describe the orientation of a part relative to other parts. The DRF is used to orient the other features of a part relative to each other and to make sure that the parts fit together as intended.
23. What is a profile tolerance?
Profile tolerance is a GD&T symbol used to define the allowable variation of a particular feature’s size and shape from its theoretical perfect form. It is used to control the form and size of a feature and to ensure that the part is made to the desired size and shape.
24. What is a runout tolerance?
Runout tolerance is a GD&T symbol used to define the allowable variation of a part from its theoretical perfect form. It is used to ensure that a part is round and concentric, and it is used to control the amount of variation of a part from its perfect form.
25. How is GD&T used in manufacturing?
GD&T is used in manufacturing to ensure that parts are made to the exact size, shape, orientation, and location specified in the design. It allows for tighter tolerances and less waste, resulting in improved accuracy and precision of the finished product. It also improves communication between engineers, designers, machinists, and other personnel involved in the manufacturing process by providing a common language for understanding and conveying design intent.
Tips on Preparing for a GD&T Interview
- Research the company’s culture and values to understand how GD&T may fit into their operations.
- Brush up on GD&T terminology and what each symbol means.
- Practice explaining GD&T concepts and principles in simple terms.
- Familiarize yourself with the different types of GD&T symbols and their applications.
- Consider any common- sense GD&T situations you may have encountered in a prior job or project.
- Prepare additional examples or exercises to share with the interviewer.
- Have a list of questions ready to ask the interviewer that demonstrate your interest in the job and GD&T.
- Anticipate any questions the interviewer may have about your work experience or qualifications.
- Create a portfolio of GD&T drawings and related documents that you can use as reference during the interview.
- Review any GD&T books or resources to refresh your knowledge and skills.
- Familiarize yourself with the GD&T standards, such as ASME Y14.5, for the interview.
- Practice using a CAD program to generate GD&T drawings.
- Practice GD&T drawing interpretation skills.
- Practice GD&T problem- solving skills.
- Prepare a professional resume and cover letter to submit along with your GD&T portfolio.
Conclusion
Overall, GD&T interview questions and answers can be difficult to prepare for. It is important to have a thorough understanding of each element of GD&T before stepping into the interview room. With practice and time spent researching the subject, you can become more confident in your ability to answer GD&T interview questions. Knowing the basics of GD&T, such as the types of GD&T symbols, the rules for applying them and the concepts of tolerancing, will go a long way to helping you ace the interview.