Going through an interview process is a nerve-wracking experience, especially when the interview is for a quality engineer role. The position requires the individual to be able to think critically and analyze data to identify areas of improvement.
In order to help you prepare for the quality engineer interview, we have created a comprehensive guide. This guide includes the most commonly asked quality engineer interview questions and answers. We have broken down the questions and answers into easy to understand sections so that you can quickly pinpoint the topics you need to focus on.
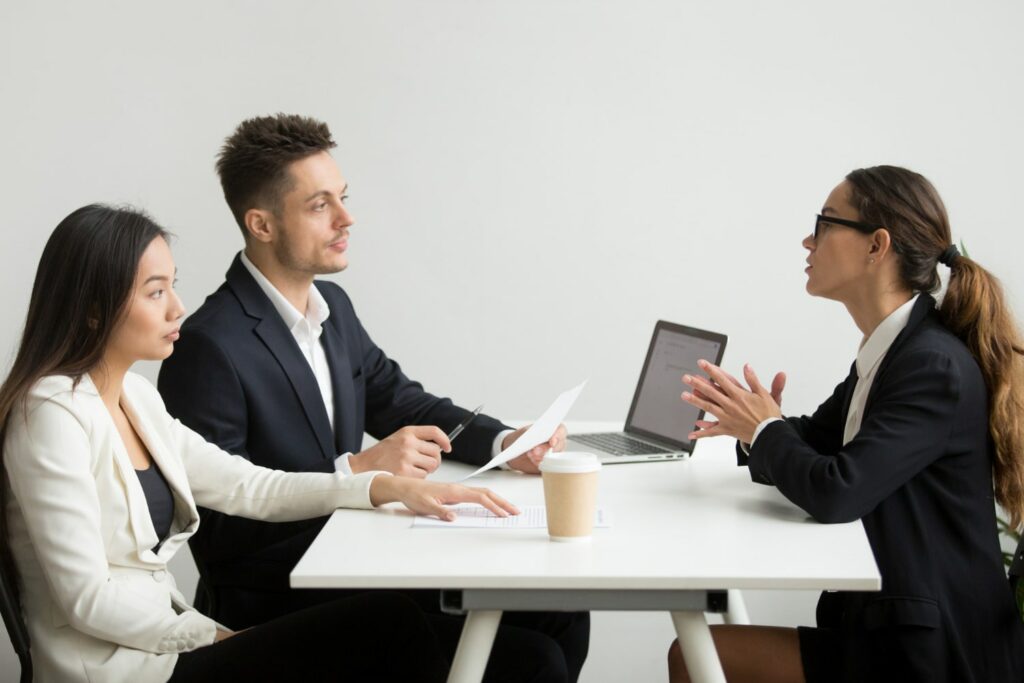
We understand that interviews can be intimidating and overwhelming. That’s why we have included various in-depth answers to the questions. We have also provided sample answers so that you can practice your responses and be prepared for any questions the interviewer might ask.
Whether you are a novice or a seasoned professional, this guide is sure to help you impress the interviewer with your knowledge and expertise in the quality engineering field. With our guide, you can be confident that you will be well-prepared for your quality engineer interview.
Overview of Quality Engineer Interview Process
A quality engineer interview process typically involves several rounds of interviews, beginning with a screening interview to determine both the candidate’s qualifications and their overall suitability. This screening interview is usually conducted over the phone, though it may be held in person. It will often include questions about the candidate’s relevant work experience, education, technical skills, and any certifications they may hold, as well as their ability to work in a team and ability to handle stressful situations.
The next round in a quality engineer interview process is typically a technical interview. This is a more in- depth conversation about the candidate’s technical and problem- solving skills. The interviewer may ask the candidate to explain their understanding of specific quality engineering principles, such as Six Sigma or ISO 9001, and to explain how they would use them in specific scenarios. The interviewer may also ask the candidate questions about their experience with specific technologies or software, such as CAD/CAM, and how they would use them to implement quality controls.
The final round of a quality engineer interview process is usually a behavioral interview. Here, the interviewer may ask questions about the candidate’s prior managerial or supervisory experience, if any, and how they handled difficult conversations or tight deadlines. The interviewer may also ask the candidate to explain how they handle feedback, criticism, and changes in project scope. The goal of this final round is to get a better feel for the candidate’s work habits, team dynamics, and work ethic.
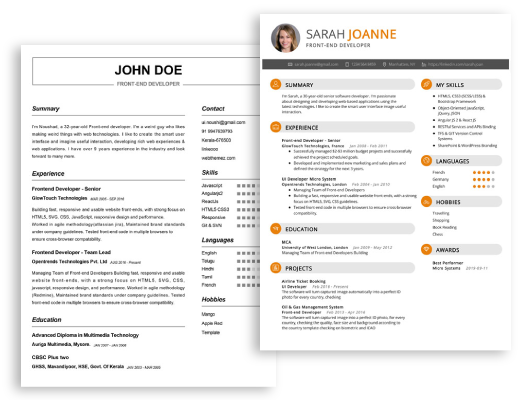
Start building your dream career today!
Create your professional resume in just 5 minutes with our easy-to-use resume builder!
Be sure to check out our resume examples, resume templates, resume formats, cover letter examples, job description, and career advice pages for more helpful tips and advice.
Top 17 Quality Engineer Interview Questions and Answers
1. What experience do you have as a Quality Engineer?
I have five years of experience in the field of quality engineering. In my current role, I am responsible for designing and executing quality assurance processes, developing test plans and performing root cause analysis. I have a strong understanding of the software development life cycle and am certified in a variety of quality assurance processes, such as ISO 9001:2015. Additionally, I have successfully implemented quality improvement initiatives and presented my findings to senior management. My experience also includes creating and implementing quality metrics, collecting and analyzing data, and developing and maintaining relationships with internal and external stakeholders.
2. Describe your approach to developing test plans?
My approach to developing test plans involves first determining the objectives of the project, and then creating a plan that outlines all the necessary steps for successful completion. This includes considering the scope of the project, the timeline, the resources needed, and the cost. I also ensure that the plans consider the risk factors and any potential issues that might arise. Once all of the components have been identified, I create a comprehensive document that outlines the entire process. This document is then used for testing and debugging, and all stakeholders are kept up to date on the progress.
3. How do you ensure that the quality standards are met?
I ensure that quality standards are met by creating and following an established set of procedures and guidelines. I also communicate regularly with stakeholders to ensure that all requirements are being met and that any potential issues are identified and addressed in a timely manner. Additionally, I utilize quality assurance tools and techniques to monitor the progress of the project and ensure that all standards are being met. This includes performing regular audits, creating reports and analyzing data to identify potential problem areas, and developing processes and procedures to address any identified issues.
4. What techniques do you use to identify root causes?
I use a variety of techniques to identify root causes, including process mapping, root cause analysis, and fault tree analysis. Process mapping is used to clearly understand the process flow and identify any areas of waste or inefficiency. Root cause analysis is used to identify the origin of the problem and determine the contributing factors. Finally, fault tree analysis is used to identify the various factors that lead to a certain outcome, in order to better understand the root cause of the issue.
5. What strategies do you use to improve quality?
I use several strategies to improve quality. First, I develop and implement quality metrics that accurately measure the progress of the project. I then utilize data analysis tools to identify areas of improvement and develop corrective action plans. Additionally, I use continuous improvement techniques such as Six Sigma and Lean Six Sigma, to identify opportunities for improvement and develop processes and procedures to address any identified issues. Finally, I maintain regular communication with stakeholders to ensure that all requirements are met and that any potential issues are addressed in a timely manner.
6. How do you handle competing priorities and multiple deadlines?
When faced with competing priorities and multiple deadlines, I prioritize each task and focus on the highest priority items first. I also use time management techniques such as task lists and To-Do lists to stay organized and ensure that tasks are completed on time. Additionally, I communicate regularly with my manager and other key stakeholders to ensure that progress is being made on all tasks and to identify any areas where additional resources may be needed.
7. How do you use data analysis to identify areas of improvement?
I use data analysis to identify areas of improvement by collecting and analyzing data from various sources, such as customer surveys, customer feedback, and process logs. I then look for patterns in the data and identify areas where performance could be improved. Additionally, I utilize statistical process control techniques to identify opportunities for improvement and develop corrective action plans.
8. How do you integrate customer feedback into the quality process?
I integrate customer feedback into the quality process by actively engaging customers and gathering their feedback throughout the life cycle. This includes conducting customer surveys, collecting customer feedback from various sources, and using customer feedback as a metric for measuring quality. Additionally, I use customer feedback to identify areas of improvement and develop corrective action plans.
9. How do you ensure customer satisfaction?
I ensure customer satisfaction by focusing on delivering quality products and services that meet or exceed customer expectations. To do this, I incorporate customer feedback into the development process and ensure that any identified areas of improvement are addressed. Additionally, I use customer feedback as a metric for measuring product quality, and review customer feedback on a regular basis to make sure that customer expectations are being met.
10. What challenges have you faced while working as a Quality Engineer?
One of the main challenges I have faced while working as a Quality Engineer is managing competing priorities and multiple deadlines. This requires me to prioritize tasks and stay organized in order to ensure that tasks are completed on time. Additionally, I have faced challenges with data collection and analysis, particularly when dealing with large datasets. To address this, I have developed strategies for gathering and analyzing data, as well as strategies for developing corrective action plans based on the data analysis.
11. How do you ensure that a product meets customer requirements?
I begin by assessing customer requirements to ensure they are well defined and understood. Then I create a test plan that outlines the objectives and scope of the testing. This test plan will include the testing tools and test cases that need to be conducted. After that, I execute the tests and record the results. Finally, I analyze the results to verify if the product meets the customer requirements. If it does, I will recommend releasing the product. If not, I will suggest further testing and/or tweaks to the product to ensure it meets the customer requirements.
12. How do you prioritize tasks as a Quality Engineer?
When prioritizing tasks I like to start by assessing the urgency of each task. This helps me to decide which tasks need to be tackled first. Then I think about the risk associated with each task. If a task carries a higher risk, it is usually something I will prioritize first. I also look at the resources available to me and the time I have to complete the task. This helps me to figure out which tasks can be accomplished within the given timeframe.
13. What methods do you use to identify defects?
In order to identify defects, I first look at customer feedback and bug reports. This can help me to identify areas that need improvement. Then I use various testing techniques, such as integration testing, system testing, and regression testing. I also use a variety of test tools to help me identify potential defects. Finally, I review the product’s code to look for any issues.
14. How do you ensure that a product meets quality standards?
I use a variety of methods to ensure that a product meets quality standards. First, I create a test plan or set of test cases that outlines the objectives and scope of the testing. This helps me to determine what tests need to be conducted. Then I execute the tests and record the results. After that, I analyze the results to verify that the product meets the quality standards. If needed, I can suggest further tests or modifications to the product to ensure it meets the standards.
15. What challenges have you faced as a Quality Engineer?
I have faced a range of challenges as a Quality Engineer. One of the biggest challenges I have faced is making sure that my tests are comprehensive and cover all of the customer’s requirements. I have also had to manage tight timelines, which can be difficult when dealing with complex projects. Additionally, I have had to ensure that the test environment is accurate and up to date in order to get reliable results.
16. How do you stay up to date with the latest trends in quality engineering?
I stay up to date with the latest trends by reading industry publications and blogs, attending conferences and workshops, and networking with other Quality Engineers and professionals. I also take online courses to stay current on the latest tools and techniques. Additionally, I participate in online discussion forums, which allow me to learn from and connect with other Quality Engineering professionals.
17. What is your approach to troubleshooting software issues?
My approach to troubleshooting software issues starts by gathering information about the issue, such as the environment, the code, and any logs. Then I reproduce the issue to confirm that it is a valid bug. Next, I conduct root cause analysis to narrow down the problem. Once I have identified the root cause, I can start to develop a solution. I then test the solution to make sure it resolves the issue, and finally deploy the solution to the customer.
Tips on Preparing for a Quality Engineer Interview
- Brush up on your knowledge of quality engineering principles, standards, and best practices.
- Prepare for questions related to past projects and experiences, including how you implemented quality engineering protocols.
- Have questions ready to ask the interviewer.
- Research the company and become familiar with their quality engineering procedures.
- Practice answering common interview questions.
- Prepare examples of how you have used quality engineering tools and processes to solve problems.
- Have a portfolio of examples of your quality engineering work and/or certificates in case the interviewer requests to see them.
- Be prepared to discuss the value- added service you can provide to the company.
- Be ready to explain how you can use quality engineering methods to improve the overall quality of the company’s products.
- Have an understanding of the latest quality engineering trends and industry developments.
- Show your enthusiasm for quality engineering and emphasize the importance of quality in all aspects of your work.
- Focus on your communication and interpersonal skills, as well as your problem- solving abilities.
- Demonstrate your knowledge of the latest software, tools, and technologies used in quality engineering.
- Discuss your ability to work collaboratively with other stakeholders.
- Show your commitment to excellence and to continuously learning about quality engineering practices.
Conclusion
Answering quality engineer interview questions with confidence and showing an understanding of the role and the industry is key to nailing an interview for a quality engineer position. With the right preparation, research and practice, you can go into your interview feeling confident and ready to make a great impression. Gathering information on the company and the job, practicing responses to common quality engineer questions, and understanding the quality engineering industry can all help you be successful in your interview.