Good Design and Tolerancing, or GD&T, is a language used to accurately communicate the design intent of a part or assembly. It is used to define the shape and size of a part, as well as how it fits and interacts with other parts. Knowing how to use and interpret GD&T is an essential skill for any mechanical engineer, and mastering it can give you a leg up when it comes to interviews.
When it comes to GD&T, the questions you will be asked in an interview can vary widely. These questions may range from the basics, such as how to interpret a GD&T symbol, to more complex concepts, such as how to use a Datum Reference Frame (DRF). Additionally, you may be asked to explain how to use GD&T to specify a part’s dimensional and geometric tolerances.
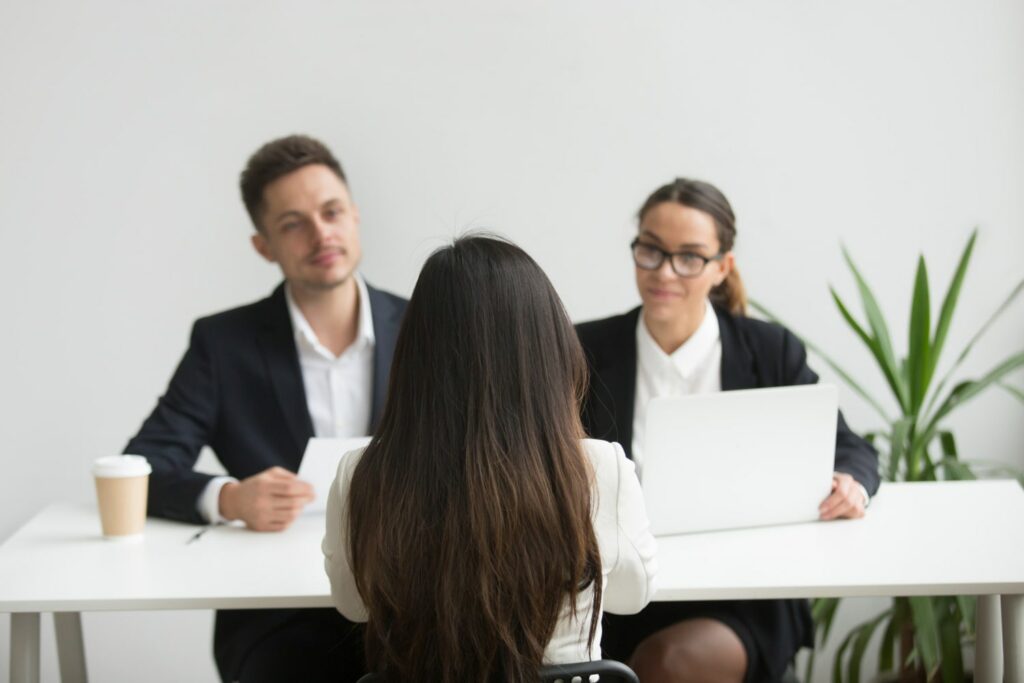
If you’re preparing for a GD&T interview, it is important to know the answers to common GD&T interview questions. This article provides a comprehensive list of GD&T interview questions and answers to help you prepare for your upcoming interview. It includes questions related to the basics of GD&T, as well as more complex topics. It also includes sample answers to help you understand the concepts and give you an idea of how to structure your own answers.
By reviewing this list of GD&T interview questions and answers, you’ll be able to gain a better understanding of the fundamentals of GD&T and be better prepared for your interview. This will help you stand out from other candidates and give you the best chance of success in your GD&T interview.
Overview of GD and T Interview Process
Geometric Dimensioning and Tolerancing (GD&T) is a language used to describe the size, shape, and position of a part in detail. Used by engineers, designers and technicians, GD&T uses symbols and notes to define the tolerances for a part. Under GD&T, all of the necessary information for part production can be communicated in a single drawing, which eliminates the need for multiple drawings, thus reducing cost and complexity.
The GD&T interview process is designed to determine the candidate’s ability to interpret and apply GD&T principles in a professional environment. In addition to having a basic knowledge of GD&T, the candidate should be able to demonstrate the ability to read engineering drawings, interpret GD&T symbols, and apply the appropriate GD&T principles. Questions may be asked in the interview to check the candidate’s mastery of the language and knowledge of application.
The GD&T interview can be divided into two sections: the basic concepts and the applied principles. During the basic concepts portion of the interview, the interviewer may ask the candidate questions about the fundamentals of GD&T. The questions may range from simple definitions, such as the purpose of GD&T, to more complex topics, such as the common GD&T symbols and the various tolerance types.
The applied principles portion of the interview typically follows the basic concepts portion. Here, the interviewer will ask the candidate to explain how certain GD&T principles would be applied to a sample drawing. The candidate should be able to read the drawing, interpret the GD&T symbols, and correctly explain the implications of the symbols to the interviewer.
Overall, the GD&T interview process is designed to evaluate the candidate’s mastery of the language and application of the GD&T principles.
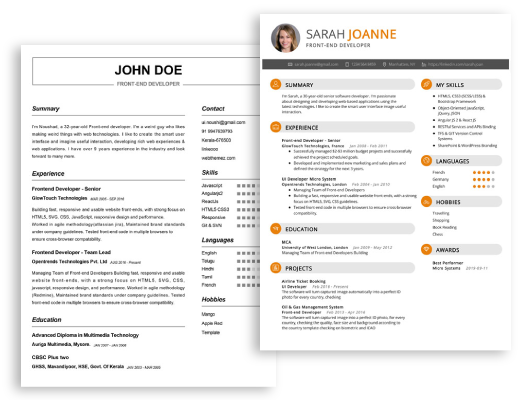
Start building your dream career today!
Create your professional resume in just 5 minutes with our easy-to-use resume builder!
Be sure to check out our resume examples, resume templates, resume formats, cover letter examples, job description, and career advice pages for more helpful tips and advice.
Top 18 GD and T Interview Questions and Answers
Q1. What is Geometric Dimensioning and Tolerancing (GD&T)?
Geometric Dimensioning and Tolerancing (GD&T) is a method of defining the relationship between a part and a drawing. It allows engineers to communicate the necessary information to manufacturers and suppliers, so the part is manufactured according to the exact specifications. GD&T is the language of drawings that allows for precise communication between engineers and manufacturers. It defines the boundary of the part and how it should function in relation to other parts. GD&T is an important tool for ensuring that parts are made accurately and consistently.
Q2. How does GD&T help improve product quality?
GD&T helps improve product quality by providing precise and clear communication between engineers and manufacturers. With the use of GD&T, engineers can specify the exact size, shape, and orientation of parts in relation to each other. This information can then be transferred to the manufacturer, who can use it to create a part that meets the engineer’s exact specifications. Additionally, GD&T helps to prevent errors during part manufacturing, as it clearly defines the tolerances of the part. By using GD&T, manufacturers have the ability to create parts that meet the engineer’s specifications, thus helping to improve product quality.
Q3. What is the purpose of GD&T?
The purpose of GD&T is to provide a standard language for engineers and manufacturers to communicate the exact size, shape, and orientation of parts in relation to each other. It allows engineers to define the exact requirements of a part, which can then be transferred to the manufacturer. This ensures that parts are made according to the engineer’s exact specifications and helps to prevent errors during part manufacturing. Additionally, GD&T helps to improve product quality by providing precise communication between engineers and manufacturers.
Q4. What is a datum?
A datum is a reference point in GD&T that is used to define the size, shape, and orientation of a part in relation to other parts. A datum is used to establish a reference point from which all other measurements and tolerances can be defined. It is important to have clear and accurate datums in order to ensure that parts are made according to the engineer’s exact specifications. Additionally, datums are used to help prevent errors during part manufacturing.
Q5. What is a basic dimension?
A basic dimension is a dimension that is used to define the size, shape, and orientation of a part in relation to other parts. Basic dimensions are used to establish the exact specifications of a part and are not subject to tolerances. They are used to define the size of a part and are the basis of all other measurements and tolerances. Basic dimensions are very important for ensuring that parts are made according to the engineer’s exact specifications.
Q6. What does tolerance mean in GD&T?
Tolerance is the acceptable amount of variation for a particular dimension or feature. In GD&T, tolerance is used to define the acceptable amount of variation from the exact specifications of a part. It is important to have clear and accurate tolerances in order to ensure that parts are made according to the engineer’s exact specifications. Additionally, tolerances are used to help prevent errors during part manufacturing.
Q7. What is a feature control frame?
A feature control frame is a notation used in GD&T to define the size, shape, and orientation of a part in relation to other parts. It is used to communicate the exact specifications of a part and also contains the tolerance and other relevant information. A feature control frame is used to define the size and orientation of a part and helps to ensure that parts are made according to the engineer’s exact specifications.
Q8. What is the difference between a datum and a basic dimension?
The main difference between a datum and a basic dimension is that a datum is used to define the size, shape, and orientation of a part in relation to other parts, while a basic dimension is used to define the exact specifications of a part. A datum is used to establish a reference point from which all other measurements and tolerances can be defined, while a basic dimension is used to define the size of a part and is not subject to tolerances. Both are important for ensuring that parts are made according to the engineer’s exact specifications.
Q9. What is tolerance stack up?
Tolerance stack up is the process of evaluating the cumulative effect of multiple tolerances on the final part dimensions. It is used to ensure that the cumulative effect of all of the tolerances does not exceed the acceptable amount of variation for a particular dimension or feature. Tolerance stack up is important for ensuring that parts are made according to the engineer’s exact specifications and helps to prevent errors during part manufacturing.
Q10. What is a true position?
A true position is a type of GD&T feature that is used to define the exact location of a hole, slot, or other feature. It is used to define the exact specifications of a part and is not subject to tolerances. A true position is important for ensuring that parts are made according to the engineer’s exact specifications and helps to prevent errors during part manufacturing.
Q11. What is a maximum material condition (MMC)?
A maximum material condition (MMC) is a type of GD&T feature that is used to define the maximum amount of material that can be present in a particular feature. It is used to define the exact specifications of a part and is not subject to tolerances. An MMC is important for ensuring that parts are made according to the engineer’s exact specifications and helps to prevent errors during part manufacturing.
Q12. What is a least material condition (LMC)?
A least material condition (LMC) is a type of GD&T feature that is used to define the minimum amount of material that must be present in a particular feature. It is used to define the exact specifications of a part and is not subject to tolerances. An LMC is important for ensuring that parts are made according to the engineer’s exact specifications and helps to prevent errors during part manufacturing.
Q13. What is the difference between a datum and an axis?
The main difference between a datum and an axis is that a datum is used to define the size, shape, and orientation of a part in relation to other parts, while an axis is used to define a line or direction. A datum is used to establish a reference point from which all other measurements and tolerances can be defined, while an axis is used to help define the orientation of a part in relation to other parts. Both are important for ensuring that parts are made according to the engineer’s exact specifications.
Q14. What is a profile tolerance?
A profile tolerance is a type of GD&T feature that is used to define the exact shape of a part. It is used to define the exact specifications of a part and is not subject to tolerances. A profile tolerance is important for ensuring that parts are made according to the engineer’s exact specifications and helps to prevent errors during part manufacturing.
Q15. What is a form tolerance?
A form tolerance is a type of GD&T feature that is used to define the exact shape of a part. It is used to define the exact specifications of a part and is not subject to tolerances. A form tolerance is important for ensuring that parts are made according to the engineer’s exact specifications and helps to prevent errors during part manufacturing.
Q16. What is a positional tolerance?
A positional tolerance is a type of GD&T feature that is used to define the exact location of a hole, slot, or other feature. It is used to define the exact specifications of a part and is not subject to tolerances. A positional tolerance is important for ensuring that parts are made according to the engineer’s exact specifications and helps to prevent errors during part manufacturing.
Q17. What is a runout tolerance?
A runout tolerance is a type of GD&T feature that is used to define the exact orientation of a part in relation to other parts. It is used to define the exact specifications of a part and is not subject to tolerances. A runout tolerance is important for ensuring that parts are made according to the engineer’s exact specifications and helps to prevent errors during part manufacturing.
Q18. What is a concentricity tolerance?
A concentricity tolerance is a type of GD&T feature that is used to define the exact location of a hole, slot, or other feature. It is used to define the exact specifications of a part and is not subject to tolerances. A concentricity tolerance is important for ensuring that parts are made according to the engineer’s exact specifications and helps to prevent errors during part manufacturing.
Tips on Preparing for a GD and T Interview
- Research the company and the role you’re interviewing for. Make sure you understand the requirements of the role and the specific GD&T qualifications that are necessary.
- Familiarize yourself with the latest GD&T standards. Read up on the principles of GD&T and any new developments in the field.
- Practice answering typical interview questions related to GD&T. Make sure you can explain your experience and qualifications in a concise and clear manner.
- Prepare examples of projects you have worked on that involved GD&T. Have a few examples of your work ready to discuss.
- Practice using drawing tools and drafting software. Be able to explain how and why you used certain drawing tools or software for a specific project.
- Prepare questions for the interviewer. You should have at least a few good questions in mind to ask the interviewer.
- Practice drawing a part from a given dimensional print. Be able to explain your approach to creating a part from a GD&T drawing.
- Demonstrate a basic understanding of Statistical Process Control (SPC). Be able to explain the importance of SPC and why it is important for GD&T.
- Practice diagramming GD&T symbols and the related terms. Make sure you are comfortable with the different GD&T symbols and terms.
- Show interest in the company and the role. Make sure you show that you are passionate about working for the company and taking on the role.
Conclusion
If you’re looking for a comprehensive guide to GD and T interview questions and answers, this blog post is a great place to start. It covers many of the topics that are commonly asked in interviews and provides detailed responses to each. With this information, you can be better prepared to ace your GD and T interview. Good luck!